Enhancing Metal Fabrication with High Pressure Die Casting Mold
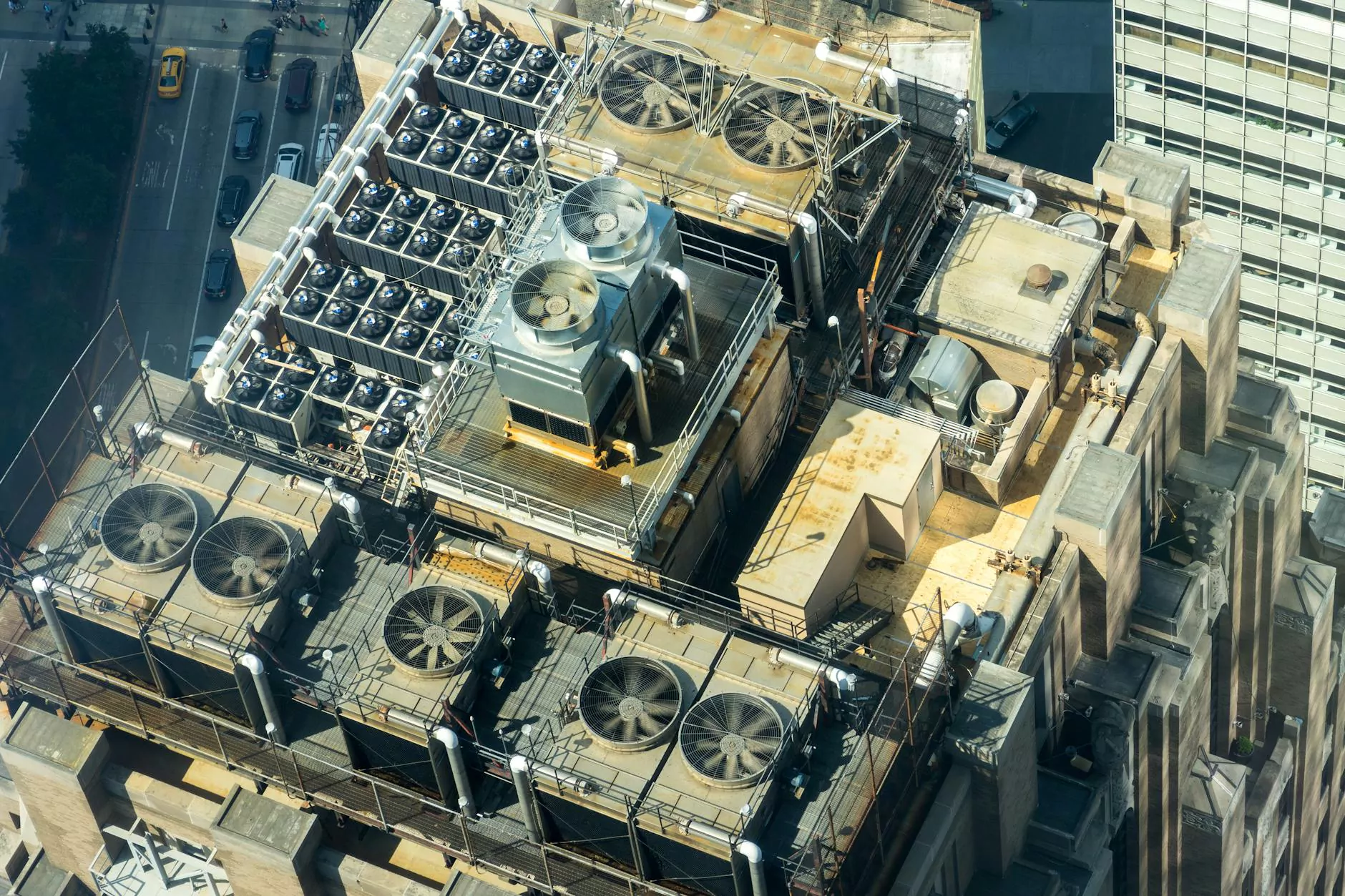
Introduction
Metal fabrication has come a long way in meeting the demands of various industries, and one of the cutting-edge technologies revolutionizing this sector is the use of high pressure die casting mold. Deepmould.net, a leading provider of metal fabrication solutions, has employed this innovative technique to provide its clients with high-quality, precision-engineered parts and components.
Benefits of High Pressure Die Casting Mold
High pressure die casting mold offers numerous benefits to metal fabricators, making it a go-to choice for businesses worldwide. Here are some key advantages:
1. Superior Precision and Accuracy
High pressure die casting mold allows for the production of complex parts with exceptional precision and accuracy. With this technique, it is possible to create parts with intricate details, tight tolerances, and consistent quality. This precision ensures that the final products meet the most stringent requirements and surpass customer expectations.
2. Cost-Efficiency
By utilizing high pressure die casting mold, metal fabricators can optimize their production processes and achieve significant cost savings. The use of reusable molds and the ability to produce parts with minimal material waste contribute to a more efficient manufacturing process. Additionally, the high production speed of this technique allows for quick turnaround times, reducing overall expenses and maximizing productivity.
3. Versatility in Material Selection
High pressure die casting mold supports a wide range of materials, including aluminum, zinc, and magnesium alloys. The versatility in material selection enables metal fabricators to meet the specific needs of diverse industries. Whether it's automotive, aerospace, electronics, or consumer goods, this technique provides the flexibility to create components from different alloys, ensuring optimal performance and durability.
4. Enhanced Structural Integrity
Components produced using high pressure die casting mold exhibit excellent structural integrity. The high pressure exerted during the casting process results in a dense and homogeneous material structure, minimizing the presence of imperfections. This enhanced structural integrity translates to parts with superior strength, reduced porosity, and improved overall performance, making them ideal for critical applications that require reliability and durability.
5. Streamlined Production Workflow
The use of high pressure die casting mold streamlines the production workflow, enabling faster and more efficient manufacturing. Its automated nature and high repeatability significantly reduce the time and effort required for each casting, resulting in increased productivity. Furthermore, the elimination of post-processing steps, such as machining or welding, saves additional time and resources.
Applications of High Pressure Die Casting Mold
The versatility of high pressure die casting mold opens up a wide range of applications across various industries. Let's take a closer look at some of these applications:
1. Automotive Industry
The automotive industry extensively utilizes high pressure die casting mold for the production of engine components, transmission parts, and structural elements. Aluminum alloys are particularly popular in this sector due to their lightweight properties, high strength-to-weight ratio, and excellent thermal conductivity. The use of high pressure die casting mold enables automotive manufacturers to create parts that contribute to fuel efficiency, safety, and overall vehicle performance.
2. Aerospace Sector
With strict performance and safety requirements, the aerospace sector benefits greatly from high pressure die casting mold. Components such as turbine blades, structural brackets, and gearbox housings can be efficiently manufactured using this technique. Aluminum and magnesium alloys, renowned for their high strength and low weight, are commonly employed to meet the stringent demands of the industry.
3. Electronics and Telecommunications
The electronics and telecommunications industries rely on high pressure die casting mold to produce precise and durable components for devices such as smartphones, laptops, and networking equipment. The use of this technique ensures the production of intricate parts that comply with strict dimensional tolerances, maintain excellent connectivity, and resist environmental factors.
4. Consumer Goods
High pressure die casting mold is also prevalent in the consumer goods industry, where it enables the manufacturing of a diverse range of products. From high-end kitchen appliances to power tools and sporting equipment, this technique ensures the mass production of components that possess exceptional quality, aesthetic appeal, and functionality.
Conclusion
Deepmould.net understands the immense value that high pressure die casting mold brings to the metal fabrication industry. Its numerous benefits, ranging from superior precision and accuracy to cost-efficiency and streamlining of production processes, make it an indispensable technology for businesses seeking an edge in today's competitive market.
Knowing the wide array of applications across industries such as automotive, aerospace, electronics, and consumer goods, it is clear why high pressure die casting mold has become a go-to choice for metal fabricators. By leveraging the advantages of this technique and partnering with a trusted provider like Deepmould.net, businesses can achieve remarkable results and stay ahead of their competitors in the ever-evolving world of metal fabrication.