The Ultimate Guide to Plastic Injection Molding for Metal Fabricators
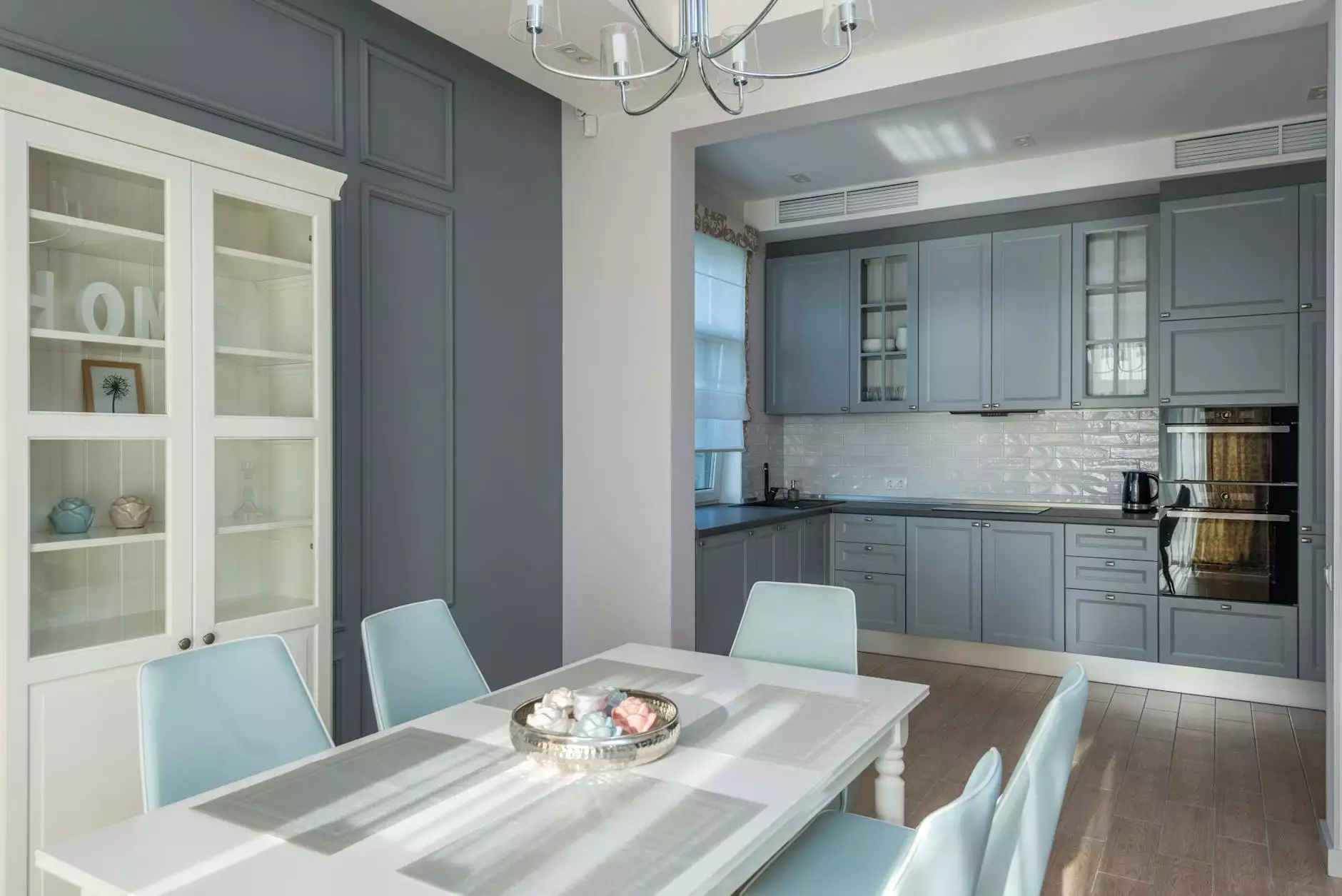
The manufacturing landscape has evolved significantly over the past few decades, with plastic injection molding becoming a cornerstone of production in numerous industries. As a fabricated alternative to traditional metal components, plastic offers unique advantages in terms of cost, weight, and versatility. In this comprehensive article, we will delve into the intricacies of plastic injection molding, its processes, benefits, and its critical role in the field of metal fabrication.
Understanding Plastic Injection Molding
Plastic injection molding is a manufacturing process that involves injecting molten plastic materials into a mold to create various shapes and parts. This method allows manufacturers to produce high-volume parts with great precision and consistency. The process can accommodate a variety of plastics, making it suitable for diverse applications in different industries, including automotive, consumer products, electronics, and more.
The Injection Molding Process
The injection molding process can be broken down into several key stages:
- Material Selection: The first step involves choosing the appropriate plastic resin, which can vary based on the application and desired properties.
- Heating: The selected plastic is heated to a molten state. This stage must be controlled carefully to prevent degradation of the material.
- Injection: The molten plastic is injected into a mold under high pressure, ensuring that all cavities are filled.
- Cooling: Once the plastic fills the mold, it is allowed to cool, solidifying into the final part shape.
- Demolding: The cooled parts are ejected from the mold, ready for inspection and potential finishing processes.
Advantages of Plastic Injection Molding
There are numerous advantages of plastic injection molding, particularly for businesses within the metal fabrication sector. Here are some of the primary benefits:
- Cost Efficiency: High production volumes lead to lower per-part costs, making it an economically viable option for mass production.
- Design Flexibility: Complex designs that are not possible with other methods can easily be achieved with injection molding.
- Fast Production: The speed of the process allows for quick turnaround times, which is crucial in competitive markets.
- Material Versatility: A wide range of plastic materials can be used, each offering unique properties such as strength, flexibility, and durability.
- Reduced Waste: The process is efficient and generates minimal waste compared to other manufacturing techniques.
The Role of a Plastic Injection Molder
A plastic injection molder plays a pivotal role in this manufacturing process. The responsibilities include:
Designing Molds
The Molder collaborates with engineers to design molds that meet specific requirements and tolerances. Precise design is crucial to ensuring the final product meets quality standards.
Setting Up Machines
Preparing the injection molding machine for production involves loading materials, setting optimal temperatures, pressures, and cycle times to ensure efficiency and quality.
Quality Control
During production, it’s essential for the molder to perform quality checks to ensure that every part produced meets the required specifications. This may involve measuring dimensions, checking for defects, and ensuring uniformity across the production line.
Applications of Plastic Injection Molding in Metal Fabrication
The integration of plastic injection molding in the metal fabrication industry provides numerous innovative solutions. Some notable applications include:
- Automotive Components: Lightweight plastic parts are increasingly used in vehicles to reduce weight and improve fuel efficiency.
- Consumer Electronics: Many electronic devices have plastic casing and parts that are manufactured using injection molding.
- Medical Devices: The use of plastics that meet health regulations allows for the creation of reliable and safe medical equipment.
- Packaging: Custom plastic packaging solutions designed through injection molding offer high durability and aesthetic appeal.
- Household Goods: Everyday items from containers to furniture often rely on plastic injection molding for their production.
Challenges in Plastic Injection Molding
While the benefits are significant, there are also challenges associated with plastic injection molding that manufacturers must navigate:
- Tooling Costs: The initial investment in mold creation can be substantial, particularly for complex designs
- Material Limitations: Not all plastics can withstand high temperatures and pressures, limiting options for certain applications.
- Overmolding Complexity: Techniques such as overmolding, where two materials are combined, can increase production time and costs.
Future Trends in Plastic Injection Molding
The advancement of technology continues to shape the future of plastic injection molding. Here are some key trends to watch for:
Sustainable Practices
As the focus on environmental sustainability grows, manufacturers are increasingly adopting recycled plastics and biodegradable materials, reshaping the market landscape.
Advanced Materials
The development of higher performance materials allows for greater functionality in increasingly complex applications, expanding the possibilities for manufacturers.
Smart Manufacturing
Integration of the Internet of Things (IoT) with injection molding processes enhances efficiency by enabling real-time monitoring and predictive maintenance of equipment.
Conclusion
In summary, plastic injection molding significantly impacts the metal fabrication industry by providing cost-effective, efficient, and versatile solutions. With the advantages it offers, alongside a skilled plastic injection molder, businesses can stay competitive in a constantly changing marketplace. By embracing technological advancements and sustainable practices, the future of plastic injection molding looks bright, promising innovation and growth for manufacturers in various sectors. For a deeper understanding of how this process can transform your production capabilities, consider partnering with experienced professionals in the field.
For more insights and services related to metal fabrication and injection molding, visit DeepMould.net.