Unlocking the Future of Precision: The Impact of CNC Machining in Metal Fabrication
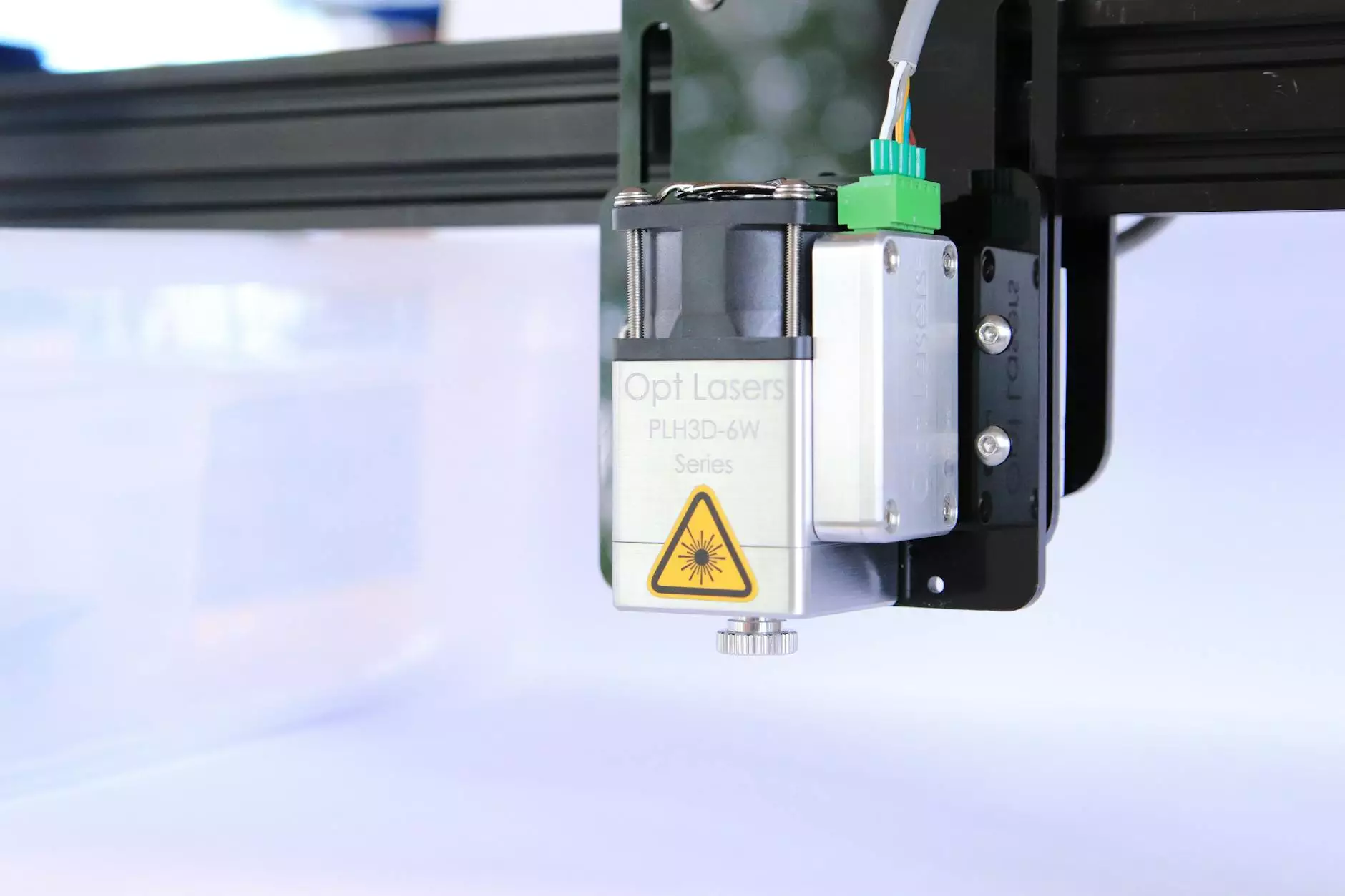
In today's competitive business environment, the quest for precision and efficiency is paramount. CNC machining has emerged as a revolutionary technology in the realm of metal fabrication, transforming how businesses approach manufacturing. This article delves into the fundamentals, benefits, applications, and future of CNC machining, providing insights for businesses looking to leverage this technology for growth and innovation.
What is CNC Machining?
CNC machining, which stands for Computer Numerical Control machining, refers to the automated control of machining tools by means of a computer. This technology allows for the precise and repeatable manufacturing of complex parts by following a set of programmed instructions. The process typically involves the use of various cutting tools and machines, such as lathes, mills, and routers, enabling the creation of intricate designs with unparalleled accuracy.
The Evolution of CNC Machining
The journey of CNC machining started in the 1940s with the development of numerical control (NC) systems. Initially, these systems were controlled via punched tape which incorporated a fixed set of commands. With advancements in technology, the introduction of computers allowed for more sophisticated control systems. Over time, the evolution of software and hardware has made CNC machining essential for modern manufacturing.
Benefits of CNC Machining
The adoption of CNC machining in metal fabrication comes with numerous advantages that can significantly enhance operational efficiency and product quality. Here are some of the key benefits:
- Precision and Accuracy: CNC machines operate with minimal human intervention, which reduces the risk of errors. This level of precision is critical for industries where tolerances are tight.
- Repeatability: Once a design is programmed into the CNC machine, it can produce the same component multiple times without deviation, ensuring consistency in production.
- Speed: CNC machining automates the manufacturing process, resulting in faster production rates, which is crucial for meeting tight deadlines.
- Complexity: CNC machines can create intricate designs that are often impossible to achieve with manual machining.
- Reduced Waste: High precision reduces material waste, making the process more cost-effective and environmentally friendly.
- Flexibility: CNC machines can be easily reprogrammed to manufacture different parts, providing versatility in product offerings.
Applications of CNC Machining
The versatility of CNC machining allows it to be applied across various industries. Here are some sectors that heavily utilize this technology:
Aerospace Industry
The aerospace industry demands high precision and reliability. CNC machining is employed to manufacture complex components such as turbine blades, housings, and brackets, ensuring they meet stringent safety and performance standards.
Automotive Industry
In the automotive sector, CNC machining is crucial for producing parts like engine blocks, transmission cases, and custom components for performance vehicles, where precision is paramount.
Medical Devices
The medical field requires extremely precise components for surgical instruments, implants, and diagnostic machines. CNC machining ensures these components meet rigorous regulatory standards and performance requirements.
Robotics
As industries move towards automation, the need for precise robotic components grows. CNC machining produces the intricate parts needed for robotic arms, sensors, and actuators.
Understanding the CNC Machining Process
The process of CNC machining consists of several stages, each critical to the final product's quality. Below is an overview of the typical workflow:
1. CAD Design
The first step involves creating a Computer-Aided Design (CAD) model of the part to be manufactured. This model includes all specifications, dimensions, and design features.
2. CAM Programming
Next, the CAD model is converted into G-code using Computer-Aided Manufacturing (CAM) software. This G-code contains the instructions that the CNC machine will follow.
3. Machine Setup
The CNC machine is then set up, which includes installing the necessary tools and fixtures, as well as loading the G-code program.
4. Machining Process
Once everything is set, the machining process begins. The CNC machine follows the programmed instructions to cut and shape the material into the desired part.
5. Quality Inspection
After machining, parts undergo inspection to ensure they meet the required tolerances and specifications. This may involve various measurement techniques and tools.
6. Finishing Operations
Finally, post-processing treatments like deburring, polishing, or coating may be applied to enhance the part’s properties and appearance.
Challenges in CNC Machining
While CNC machining offers numerous benefits, it is not without its challenges. Businesses must navigate various hurdles to fully harness its potential:
- High Initial Costs: The investment in CNC machinery and software can be substantial, which may deter some businesses from adopting this technology.
- Training Requirements: Operating CNC machines requires skilled personnel who are well-versed in programming and machine operation, necessitating ongoing training and development.
- Maintenance: Regular maintenance is crucial to ensure CNC machines remain operational and produce high-quality parts. Neglecting maintenance can lead to costly downtime.
Choosing the Right CNC Machining Partner
For businesses looking to integrate CNC machining into their operations, finding the right partner is crucial. Here are some essential factors to consider when selecting a CNC machining provider:
- Experience and Expertise: Look for a company with a proven track record in CNC machining and experience in your industry.
- Technology and Equipment: Ensure the provider uses up-to-date machinery and software to achieve high levels of precision and efficiency.
- Quality Assurance: Verify the company has strong quality control processes in place to guarantee that every part meets your specifications.
- Customer Support: Reliable customer support is essential for addressing any issues that may arise during production.
The Future of CNC Machining
The future of CNC machining looks promising, driven by advancements in technology and an increasing demand for high-quality manufacturing solutions. Key trends to watch include:
1. Automation and Industry 4.0
As the manufacturing landscape evolves, integrating IoT (Internet of Things) technology with CNC machines will enable smarter factories that optimize production efficiency and reduce waste.
2. Advanced Materials
The development of innovative materials such as composites and advanced alloys will expand the capabilities of CNC machining, allowing for the creation of stronger and lighter components.
3. Sustainability Initiatives
With a growing emphasis on sustainability, CNC machining processes will adapt to reduce energy consumption and minimize environmental impact.
Conclusion
CNC machining is more than just a technological advancement; it is a vital component in the future of metal fabrication. By embracing the precision, efficiency, and versatility that this technology offers, businesses can significantly enhance their production capabilities. As we move forward, companies like Deep Mould are poised to lead the charge, implementing cutting-edge CNC solutions to keep pace with the rapidly evolving manufacturing landscape.
For businesses looking to thrive in the ultracompetitive market, investing in or partnering with CNC machining solutions is no longer optional but a strategic necessity.