The Leading Plastic Tooling Manufacturer: Revolutionizing Metal Fabrication
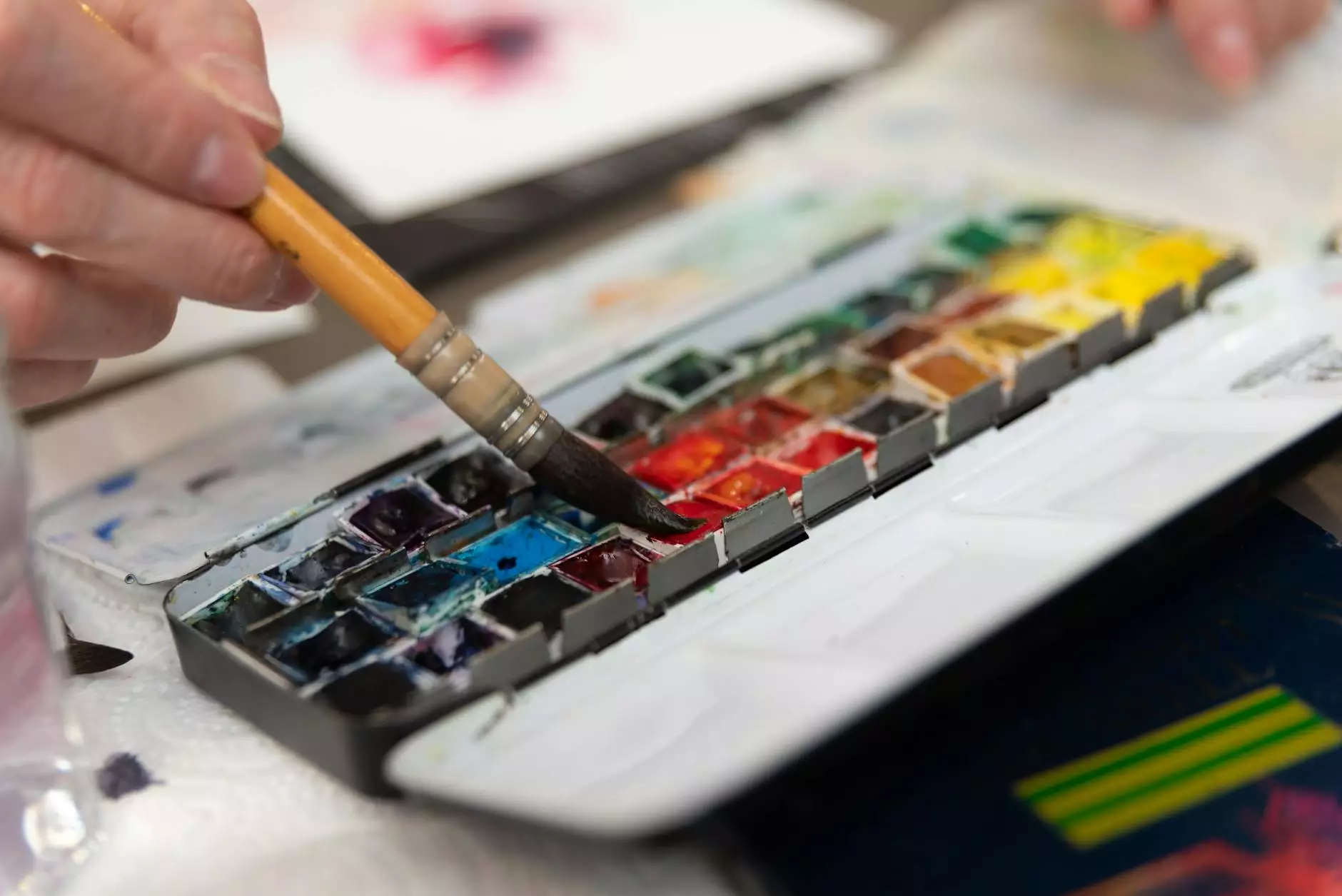
In the competitive landscape of today's manufacturing industry, the demand for exceptional quality and efficiency is at an all-time high. One of the key players making remarkable strides in this domain is DeepMould.net, a premier plastic tooling manufacturer. This article delves into the intricate processes, technological advancements, and unparalleled services provided by DeepMould, illustrating how they redefine the standards in metal fabrication.
Understanding Plastic Tooling and Its Importance
The term plastic tooling refers to the engineering process and manufacturing of tools or molds that are used for creating plastic parts. This is crucial in the production of various products ranging from automotive components, consumer goods, to electronics. As a plastic tooling manufacturer, DeepMould.net plays a vital role in the following areas:
- Precision Engineering: Every mold is engineered to meet exact specifications, ensuring high-quality production.
- Cost-Effectiveness: Creating molds that can be reused reduces manufacturing costs significantly.
- Speed: Using efficient tooling can drastically reduce production time.
Innovative Techniques in Plastic Tooling
At DeepMould, innovation is at the heart of everything they do. The company adopts advanced techniques to enhance the tooling process:
1. Advanced CAD/CAM Systems
Computer-Aided Design (CAD) and Computer-Aided Manufacturing (CAM) systems are seamlessly integrated into the design process. This allows for high levels of customization and precision:
- Three-dimensional modeling: Enables intricate designs to be both visualized and adjusted in real-time.
- Efficiency: Minimizes errors and streamlines production timelines by ensuring every detail is crafted accurately.
2. 3D Printing Technology
The incorporation of 3D printing technology revolutionizes prototyping and tooling:
- Rapid prototyping: Allows for quick revisions based on client feedback, ensuring that expectations are met efficiently.
- Reduced Waste: 3D printing significantly cuts down on material use, making the process more sustainable.
3. Modular Tooling Systems
By utilizing modular tooling systems, DeepMould enables flexible manufacturing processes:
- Scalability: These systems allow for easy adjustments in production capacity as demand fluctuates.
- Versatility: Manufacturers can produce a wider range of products with less investment in new tools.
Quality Assurance at DeepMould.net
Quality assurance is integral to the operations of DeepMould.net. The company employs a rigorous testing regime to ensure that each tool meets industry benchmarks:
- Quality Control Team: A dedicated team of specialists inspects every mold and tool.
- Client Collaboration: Engaging clients during the quality assurance phase helps to align the product with their specific needs.
Commitment to Sustainability
In recent years, the manufacturing industry has faced increasing pressure to adopt eco-friendly practices. As a responsible plastic tooling manufacturer, DeepMould.net is committed to sustainable practices:
- Recycling Materials: DeepMould utilizes recyclable materials whenever possible.
- Energy Efficiency: The company employs energy-saving machinery that reduces the carbon footprint of their operations.
Industry Applications of Plastic Tooling
DeepMould provides tooling solutions across a broad spectrum of industries. Here are some of the primary applications:
1. Automotive Industry
DeepMould supplies tooling for various automotive components, contributing to:
- Efficient Production: Streamlining the manufacturing processes of car parts.
- Quality Parts: Ensuring every component meets safety and performance standards.
2. Consumer Electronics
With the rapid advancement of technology, consumer electronics require highly sophisticated tooling:
- Precision Component Manufacturing: Ensuring optimal performance in digital devices.
- Compact Designs: Facilitating the creation of smaller, lightweight devices.
3. Medical Devices
The medical industry requires high-quality standards and reliability. DeepMould provides tooling solutions for:
- Critical Components: Manufacturing reliable, safe, and efficient medical devices.
- Compliance: Ensuring compliance with stringent healthcare regulations.
Customer-Centric Approach
At the core of DeepMould's operations is a deep commitment to their clients. From the initial consultation to the final delivery of a product, every step is designed with the client's needs in mind:
- Personalized Solutions: Custom tooling solutions tailored to specific applications.
- Ongoing Support: Continuous support post-production to address any challenges or adjustments.
Conclusion
In conclusion, DeepMould.net stands out as a leading plastic tooling manufacturer dedicated to excellence in metal fabrication. Through innovative techniques, a commitment to quality, and a focus on sustainability, they not only meet industry expectations but often exceed them.
As the demand for high-quality plastic tooling continues to rise, having a partner like DeepMould makes all the difference. Whether you are in the automotive, consumer electronics, or medical sectors, partnering with DeepMould ensures that you access the best practices in tooling manufacturing.
For more information on how DeepMould.net can enhance your operations through exceptional tooling solutions, visit our website and discover the future of manufacturing.