Understanding Die Casting: The Future of Metal Fabrication
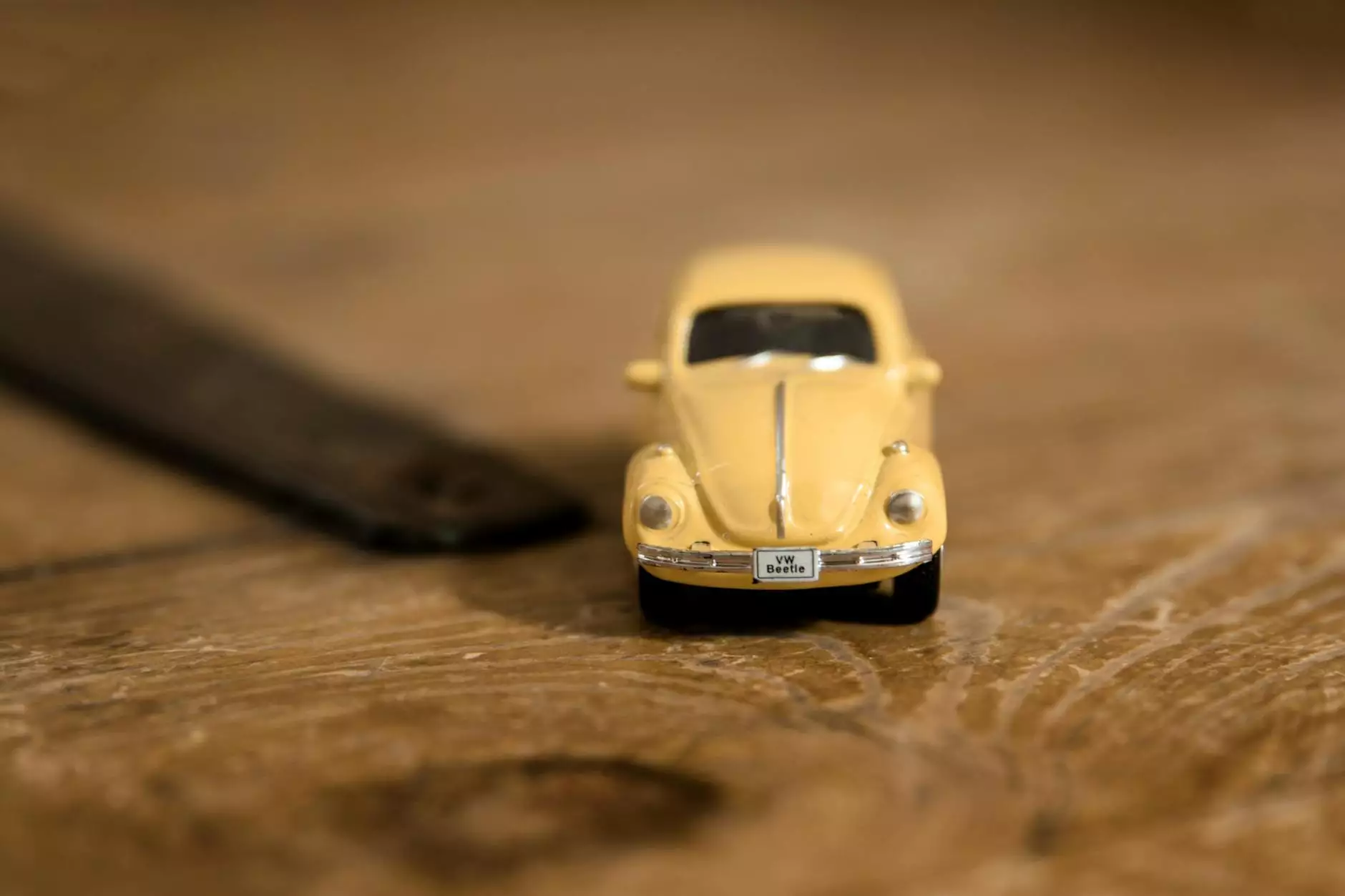
Die casting stands at the forefront of the metal fabrication industry, merging precision with efficiency to produce high-quality metal parts. As a leading process in the manufacturing realm, die casting is essential for various applications, from the automotive industry to innovative electronics. In this comprehensive article, we explore what die casting is, its processes, benefits, applications, and why your business should consider this method for metal fabrication.
What is Die Casting?
Die casting is a metal casting process that involves forcing molten metal under high pressure into a mold cavity. This process results in precise and intricate components that possess excellent surface finishes and dimensional accuracy. The molds used in die casting, referred to as dies, are made from durable materials, often steel or iron, to withstand the high pressures and temperatures involved.
The Die Casting Process Explained
The die casting process can be broken down into several key steps:
- Preparation: The process begins by preparing the die, which is pre-heated to a specific temperature to prevent premature solidification of the molten metal.
- Melt Metal: The chosen metal, often aluminum, zinc, or magnesium, is melted in a furnace until it reaches a molten state.
- Injection: Using a high-speed injection system, the molten metal is injected into the die at high pressure, filling the mold cavity quickly and completely.
- Cooling: Once the die is filled, the molten metal is allowed to cool and solidify, typically within a few seconds to minutes.
- Ejection: After solidification, the die is opened, and the part is ejected from the mold.
- Finishing: Lastly, secondary processes such as machining, surface treatment, or coating may be performed to achieve the desired specifications.
Types of Die Casting
Die casting can be categorized into two main types:
- Gravity Die Casting: This method relies on the force of gravity to fill the mold with metal. It is generally used for larger, less complex parts.
- Pressure Die Casting: In this more common method, molten metal is injected into the die under high pressure, allowing for the production of intricate and detailed parts.
Benefits of Die Casting
The adoption of die casting offers numerous benefits that are crucial for manufacturers and businesses:
- High Precision: Die casting provides exceptional dimensional accuracy, reducing the need for post-manufacturing machining.
- Complex Geometries: This method allows for the production of intricate designs that may be challenging or impossible to achieve through other manufacturing processes.
- Cost-Effectiveness: While the initial setup cost can be high, die casting is cost-effective for large production runs due to reduced labor and material waste.
- Surface Finish: Parts produced through die casting often have a smooth surface finish, which may require less finishing work.
- Material Versatility: A wide range of metals, including aluminum, zinc, and magnesium, can be utilized in the die casting process.
Applications of Die Casting
The applications of die casting span numerous industries, illustrating its versatility and importance:
1. Automotive Industry
In the automotive industry, die casting is used extensively to manufacture complex components such as transmission cases, engine blocks, and wheel rims. The precision and strength of die-cast parts contribute significantly to vehicle performance and safety.
2. Aerospace
Die casting plays a crucial role in the aerospace sector, where lightweight and high-strength components are essential. Parts such as airframe components and housings for avionics are often produced through this process.
3. Electronics
The electronics industry utilizes die casting for creating enclosures, connectors, and other components due to their excellent thermal and electrical conductivity.
4. Appliances
Household appliances often feature die-cast parts, such as housings, frames, and internal components, benefiting from durability and aesthetic appeal.
5. Industrial Equipment
Many industrial machines and equipment require rugged, reliable parts that can withstand wear and tear, making die casting a preferred choice for manufacturers.
Quality Control in Die Casting
Ensuring quality in the die casting process is paramount. Companies like Deep Mould have instituted stringent quality control measures throughout production:
- Material Testing: Raw materials are tested for purity and composition before use.
- Process Monitoring: Advanced software systems monitor variables such as temperature and pressure during the injection phase.
- Inspection: Finished products are inspected for dimensional accuracy and surface integrity using state-of-the-art equipment.
The Future of Die Casting
As industries evolve, so does the die casting process. Technological advancements, such as automation and improved materials, are driving efficiency and effectiveness in die casting. With the continued demand for high-performance, lightweight, and durable components, die casting remains a vital process in modern manufacturing.
Why Choose Deep Mould for Die Casting?
Choosing the right partner for die casting is crucial for the success of your projects. At Deep Mould, our commitment to quality, efficiency, and customer satisfaction sets us apart:
- Expertise: Our team possesses extensive experience in die casting, ensuring you receive exceptional service and products.
- State-of-the-Art Technology: We invest in the latest machinery and techniques to deliver superior products.
- Custom Solutions: We offer tailored services that meet the unique needs of each client.
- Competitive Pricing: Our streamlined processes and bulk production techniques reduce costs significantly.
Conclusion
In conclusion, die casting is more than just a method; it is a pivotal player in the realm of metal fabrication. With its numerous advantages, versatility, and a wide range of applications, die casting offers manufacturers a powerful tool for creating high-quality metal parts efficiently. As we look to the future, the innovations within die casting are set to redefine manufacturing standards across industries. For businesses seeking reliable partners in this field, Deep Mould offers the expertise and technology needed to excel. Embrace the future of manufacturing—embrace die casting.