Understanding Die Casting Dies: A Comprehensive Guide
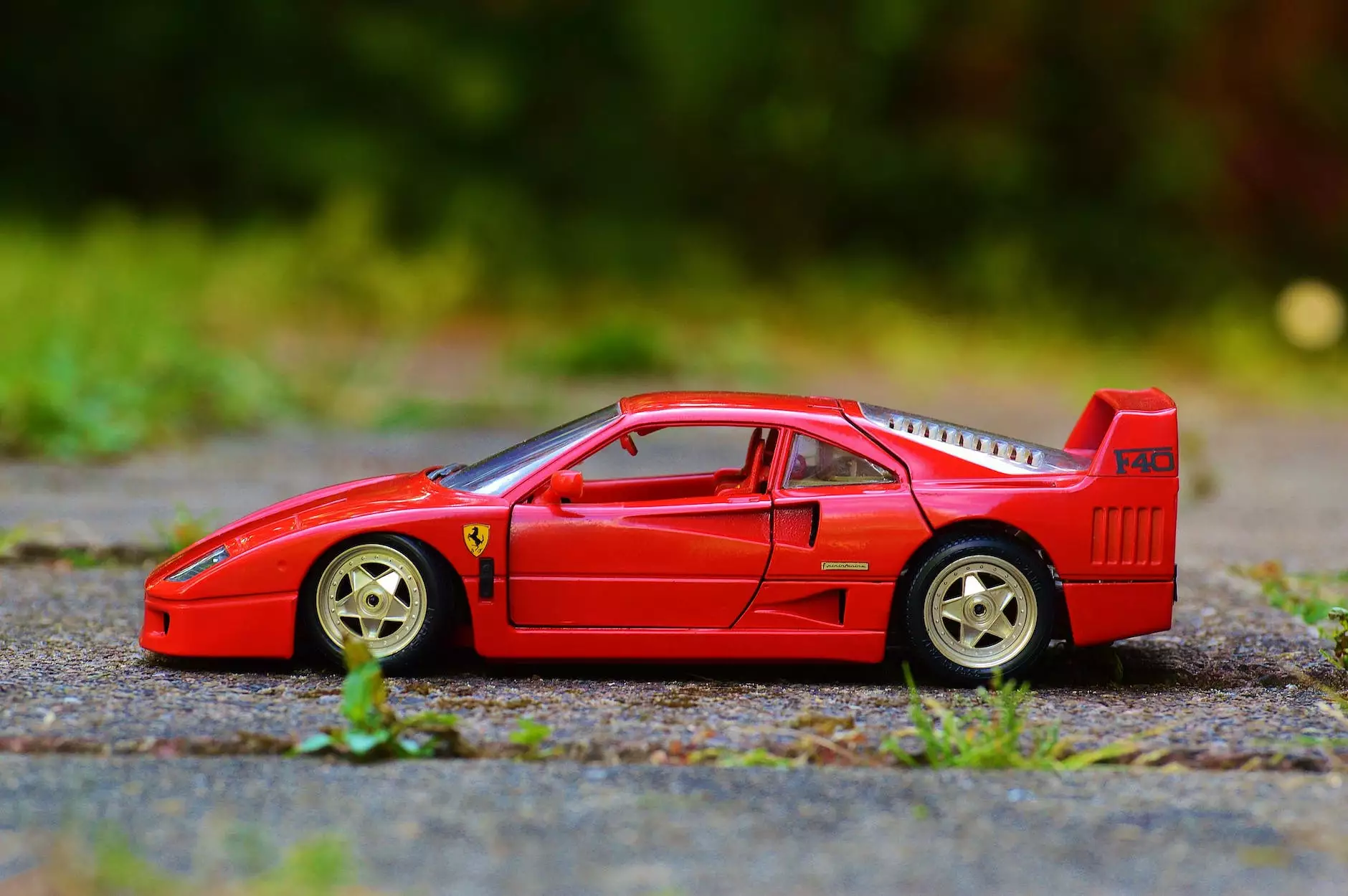
In the competitive landscape of metal fabricators, one of the key components that ensures efficiency and quality in production is the die casting dies. These tools are indispensable in the manufacturing process, allowing for the creation of precise and complex metal components. This article delves deep into the significance of die casting dies, their types, manufacturing processes, and their impact on the industry, particularly focusing on our expertise at DeepMould.net.
What Are Die Casting Dies?
Die casting dies are specialized tools used in the die casting process, which is a metal casting process characterized by forcing molten metal under high pressure into a mold cavity. This process is critical in shaping metal into intricate designs for a variety of applications. The die castings are widely utilized across multiple industries, including automotive, aerospace, electronics, and consumer goods, proving their versatility and reliability.
The Importance of Die Casting Dies in Manufacturing
Die casting dies play a crucial role in the manufacturing process, offering numerous advantages that enhance the overall efficiency and quality of production:
- Precision: Die casting allows for high precision in the dimensions of the finished products, making it ideal for applications that require tight tolerances.
- Complex Shapes: The ability to create complex shapes reduces the need for secondary machining processes, lowering overall production costs.
- Surface Finish: Die casting typically produces parts with a good surface finish that often requires minimal post-processing.
- Material Efficiency: The die casting process minimizes material waste and allows for efficient use of metal resources.
- High Volume Production: Dies can produce thousands of pieces quickly, making it a cost-effective option for large-scale production.
Types of Die Casting Dies
There are two primary types of die casting dies that are commonly used:
1. Single Cavity Die
A single cavity die allows for the production of one part per cycle. This type of die is often used for custom components or low-volume production runs, where quality and precision are paramount.
2. Multi Cavity Die
Multi cavity dies enable the production of several parts in a single cycle. This is particularly beneficial for high-volume production as it maximizes the productivity of the die casting process, reducing the cost per part.
The Die Casting Process: Step by Step
The die casting process involves several critical steps that ensure the production of high-quality metal components:
- Preparation: The process begins with preparing the die, which involves cleaning and applying a lubricant to ensure the molten metal flows smoothly and the finished part can be easily ejected.
- Melting the Metal: The metal is then heated to its melting point, often using induction furnaces, until it reaches a viscosity suitable for casting.
- Injection: The molten metal is injected into the die at high pressure, filling the cavity quickly to achieve a complete mold filling.
- Cooling: Once the die is filled, the metal cools and solidifies, taking the shape of the mold.
- Ejection: After the metal has solidified, the die opens, and the newly formed part is ejected.
- Trimming: Any excess material (known as flash) is trimmed away to produce the final component.
Materials Used in Die Casting
The choice of material in the die casting process is fundamental to the characteristics of the final product. Common materials include:
- Zinc: Known for its high strength, corrosion resistance, and lower casting temperatures.
- Aluminum: Offers lightweight and excellent corrosion resistance; ideal for automotive and aerospace applications.
- Magnesium: The lightest structural metal, preferred for weight-sensitive applications.
- Copper: Provides superior strength and is often used in electrical components.
Quality Control in Die Casting
Maintaining quality in the die casting process is paramount. Various methods are employed to ensure that parts meet the required standards, including:
- Dimensional Checks: Regular measurements are taken to ensure parts conform to required dimensions and tolerances.
- Visual Inspection: Surface defects, such as porosity and blemishes, are inspected to meet aesthetic and functional criteria.
- Non-Destructive Testing: Techniques like ultrasonic testing help identify internal defects without damaging the part.
The Future of Die Casting
The die casting industry is evolving, with advancements in technology dramatically enhancing production processes. Here are some trends shaping the future of die casting dies:
1. Automation and Robotics
Automation in die casting processes is on the rise. The integration of robotics facilitates quicker cycle times, higher precision, and decreased labor costs.
2. Sustainable Practices
As industries move toward sustainability, die casting manufacturers are focusing on reducing waste, recycling metals, and improving energy efficiency throughout the production process.
3. Advanced Materials
Ongoing research into new alloys and composites is enabling the production of parts with enhanced properties, leading to broader applications for die cast components.
Choosing the Right Die Casting Partner
For businesses looking to invest in die casting, choosing the right partner is crucial. Factors to consider include:
- Experience: A partner with a proven track record will likely understand your needs better and deliver quality results.
- Technology: The use of advanced technology can greatly influence the efficiency and quality of the production process.
- Capabilities: Ensure the partner offers a comprehensive range of services, from design to prototyping and production.
Conclusion
In conclusion, the significance of die casting dies in the metal fabricators industry cannot be overstated. Their ability to produce high-quality, complex components efficiently has made them a favored choice across various sectors. As technology advances, the die casting process is becoming even more efficient and cost-effective, ensuring that it remains a cornerstone of modern manufacturing. For businesses looking to leverage the advantages of die casting, partnering with experts like DeepMould.net can pave the way for success in your manufacturing endeavors.