The Power of Precision Injection Molding in Today's Business Landscape
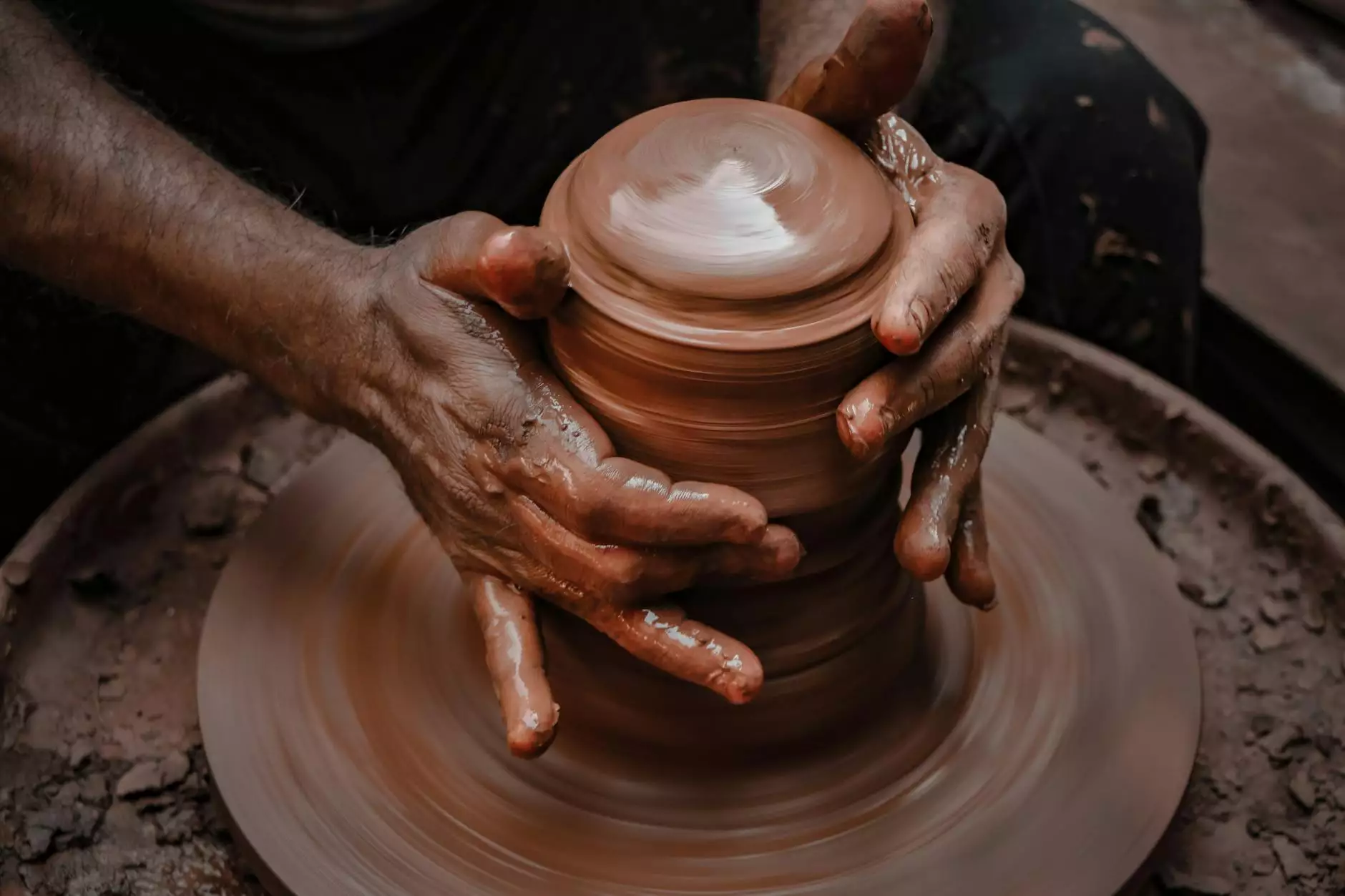
Precision injection molding has revolutionized the manufacturing sector over the last few decades. This advanced process allows for the production of extremely tight tolerance and complex geometries that are critical for modern applications. With the continuous demand for high-quality parts in various industries, including automotive, medical, and consumer goods, understanding the nuances of this technique is paramount for businesses looking to maintain competitiveness and efficiency.
What is Precision Injection Molding?
Precision injection molding is a highly sophisticated manufacturing process used to produce detailed and high-tolerance plastic parts. It involves injecting molten thermoplastic or thermosetting material into a precision-engineered mold under controlled pressure and temperature conditions. This process is characterized by its ability to create intricate designs with exceptional repeatability, making it ideal for high-volume production runs.
Key Advantages of Precision Injection Molding
The adoption of precision injection molding in manufacturing comes with numerous advantages:
- High Accuracy: Tightly controlled conditions ensure that each part produced meets exact specifications.
- Repeatability: Once a mold is created, thousands of identical parts can be produced flawlessly.
- Cost-Effectiveness: While the initial tooling can be expensive, mass production leads to reduced costs per unit.
- Material Versatility: A wide range of materials can be used, including engineering-grade plastics that have specific properties such as strength, flexibility, and heat resistance.
- Sustainability: Precision injection molding is designed for efficient material use, minimizing waste and energy consumption.
Applications of Precision Injection Molding
Precision injection molding is versatile and finds applications across various industries:
1. Automotive Industry
In the automotive sector, precision injection molding is used to produce parts such as dashboard components, lens covers, and complex assemblies. The ability to meet strict safety and performance standards makes it indispensable for manufacturers aiming to enhance vehicle reliability and efficiency.
2. Medical Devices
Medical instruments, surgical trays, and drug delivery systems are often manufactured using precision injection molding. The healthcare industry benefits from the process’s ability to sustain high hygienic standards and biocompatibility, ensuring patient safety.
3. Consumer Products
Consumer goods like electronics housings, kitchen utensils, and children's toys are commonly produced via precision injection molding. This process allows for innovative designs and colors that appeal to consumers, enhancing marketability.
4. Industrial Applications
Industrial components, including valves, fittings, and other machinery parts, take advantage of the durability and precision offered by this method, ensuring maximum performance and life expectancy under demanding conditions.
How Precision Injection Molding Works
The precision injection molding process consists of several key steps:
1. Design and Prototyping
The journey begins with creating a detailed design using Computer-Aided Design (CAD) software. Prototypes are often created to evaluate function and design integrity before finalizing the mold.
2. Mold Creation
Once the prototype is approved, a high-precision mold is manufactured, usually from steel or aluminum. The quality of the mold directly impacts the final product's quality, making this step crucial.
3. Injection Phase
Molten plastic is injected into the mold cavity under high pressure. This is the most critical phase, as the temperature and pressure must be meticulously controlled to ensure the material fills the mold completely without defects.
4. Cooling and Solidification
After the material has filled the mold, it is allowed to cool and solidify. The cooling time can vary depending on the complexity of the part and the type of material used.
5. Ejection
Once solidified, the mold opens, and the finished part is ejected. Automated systems often assist with this step to improve efficiency and reduce labor costs.
Challenges in Precision Injection Molding
Despite its numerous benefits, precision injection molding also presents some challenges that businesses must navigate:
1. Initial Costs
The initial investment for mold creation can be substantial. For small businesses or startups, this can pose a considerable barrier to entry.
2. Lead Time for Tooling
The lead time for designing and producing molds can be lengthy, impacting time-to-market for new products.
3. Material Limitations
While there is a broad range of materials available, not all materials are suitable for precision injection molding. Each material has unique properties that can influence the molding process and final product quality.
Future Trends in Precision Injection Molding
As industries evolve, so does the demand for more advanced manufacturing techniques. Precision injection molding is no exception. Here are some emerging trends that may shape the future of this process:
1. Integration of Automation and Robotics
Automating the precision injection molding process enhances efficiency and productivity, reduces human error, and allows for higher production rates.
2. Advanced Material Development
Continued innovation in materials, including biodegradable and high-performance polymers, is expected to expand the possibilities for precision injection molding applications.
3. Industry 4.0 and Smart Manufacturing
Integrating IoT technologies into injection molding processes will facilitate real-time monitoring and predictive maintenance, thereby reducing downtime and improving overall efficiency.
Conclusion: Embracing Precision Injection Molding for Business Success
With its ability to produce complex, high-tolerance components at scale, precision injection molding offers businesses in various sectors an unparalleled opportunity to innovate and grow. By leveraging the advantages of this process, companies positioned in the metal fabrication market, such as those represented by deepmould.net, can not only meet the evolving demands of their customers but also pave the way for future advancements in manufacturing.
Investing in advanced technologies and adapting to the trends of precision injection molding will ensure that businesses remain competitive and relevant in an ever-changing marketplace. The key takeaway is clear: harnessing the power of precision injection molding can substantially drive operational efficiencies, enhance product quality, and ultimately lead to higher profitability.